
A Digital Journal - San Francisco Public Works
In the Works
January 2024
Super sturdy, resilient to earthquakes and fire and more environmentally friendly than concrete and steel, a new generation of a fabricated wood product, known as mass timber, is gaining popularity in building construction and getting traction with San Francisco Public Works architects involved with civic projects.
FEATURE STORIES
Branching out: How Public Works Is
Leading a Green Building Movement
From the industrial reaches of the Bayview to a public golf course clubhouse on the western end of Golden Gate Park, a wood construction renaissance is taking root in the Bay Area – and our architects are helping drive the revival.

On the Right Road to
Smoother Streets
San Francisco’s strategic approach to maintaining roads has put the City’s independently rated Pavement Condition Index (PCI) score at the top among large Bay Area cities.

Volunteers Show Up Strong
to #LoveOurCity
More than 125 community volunteers helped us kick off the 2024 season of Love Our City: Neighborhood Beautification Day in the Richmond District.

Sixth Annual Collaborative
Partnering Awards
We hosted the 6th annual Collaborative Partnering Awards ceremony, which recognized nine City and County of San Francisco building and infrastructure projects that demonstrated collaborative partnering.


The cross-laminated timber roof at the new Golden Gate Park Golf Course Clubhouse takes shape.
Branching Out:
How Public Works Is Leading
a Green Building Movement
From the industrial reaches of the Bayview to a sprawling government campus on the Peninsula and a public golf course clubhouse on the western end of Golden Gate Park, a wood construction renaissance is taking root in the Bay Area – and San Francisco Public Works architects are helping drive the revival.
In the wake of statewide code changes that are making it easier to incorporate mass timber construction elements into new projects and behind a growing push to build more sustainably, the architects are tapping into a building technique that promises quicker turnarounds, produces more welcoming facilities and, perhaps most importantly, uses emission-storing materials to help combat global warming.
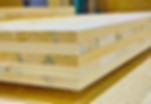
Cross-laminated timber is factory-produced by stacking and gluing lumber boards together.
Think of mass timber as plywood on steroids – layers of wood bonded together in large, sturdy pieces to handle heavy structural loads in building construction, delivering a bounty of benefits.
"Building is a carbon-intensive activity, just in general, and the more that we can reduce our carbon footprint in how we build – I think that's a really responsible thing for us to do,” said Paul De Freitas, a Public Works architect who is involved with the department’s mass timber initiative.
“Mass timber is probably what gives us the most opportunity to do that by reducing our use of concrete, reducing our use of steel,” he added.

Buildings as "energy hogs"
Concrete and steel, ubiquitous in modern-day construction, are significant drivers of greenhouse gas emissions, specifically carbon dioxide, also known as CO2. Those emissions further supercharge our climate change crisis.
“Buildings are the biggest energy hogs on earth,” said Julia Laue, Public Works’ Bureau of Architecture manager. “Buildings use the most energy of anything, from cradle to grave.”
According to the Massachusetts Institute of Technology’s Climate Portal, construction materials account for 9% of global greenhouse gas emissions from energy use – more than the energy emissions of the entire European Union.

Source: Environmental and Energy Study Institute (EESI) Fact Sheet | Building Sustainably: Mass Timber (September 2023)
The act of making cement requires a tremendous amount of energy and releases a lot of CO2 in the process, making it “one of the most carbon-intensive things we do on the planet,” De Freitas said.
Similarly, producing, shipping and recycling steel requires copious amounts of energy. Much of today’s steel is recycled content, De Freitas said. But melting down steel and repurposing it is often achieved by burning coal. “So it's a pretty dirty process,” he said.
And the building industry’s appetite for concrete and steel isn’t slowing down anytime soon.
“Housing and commercial construction account for more than half of global steel demand and, in the U.S., over 40 percent of concrete use,” according to the Massachusetts Institute of Technology’s Climate Portal.
But there is a greener way.
Mass timber construction makes use of an important feature of trees: their amazing ability to capture and store carbon dioxide.
“Those trees absorbed carbon from the atmosphere as they grew,” De Freitas said. “When you harvest them and process them into a product, you're permanently sequestering that carbon.”
The key is that the trees are specifically grown to be used for construction and sustainably harvested and managed.
The Forest Stewardship Council, headquartered in Germany and governed by a global network of more than 1,000 individuals and member organizations, has created a certification system to verify sustainable sourcing of forest products.
“They kind of manage how you manage the forest product,” De Freitas said.
Among other things, their “FSC” label signifies that trees were harvested responsibly so there is no net loss of forest over time. “Forests with irreplaceable values, such as old-growth forests, are identified and maintained,” according to the organization’s website.

Source: Forest Stewardship Council
What trees are used for mass timber construction usually differs based on region. In the southern United States that might mean more southern pines, whereas the West Coast typically makes use of Douglas fir.
They normally have one thing in common: “They’re soft woods,” De Freitas said. “They all grow super, super fast and they’re easily regenerated.”

Mass timber, past and present
The concept of mass timber construction is not new.
“Mass timber is a new name for modern interpretations of what used to be called heavy timber construction,” De Freitas said. “Heavy timber goes back a really long time and you’d see lots of old buildings in San Francisco that used to have brick walls and they’d have big, heavy sawn timber beams inside.”
Later on, there was glue-laminated timber. Instead of huge logs, De Freitas said, you could still get really big spans and cover a lot of areas by gluing together smaller pieces and making them into a bigger beam.
“And that was used for decades,” he said. “The biggest kind of evolution of that lately has been with products that make slabs out of wood.”
Enter cross-laminated timber, currently the most popular variation of mass timber construction.
Here’s how it works: Picture layered lumber boards, essentially two-by-fours, stacked on top of each other in alternating directions, at 90-degree angles, and glued together – much like plywood. That allows for the creation of a giant slab, 12 feet by 40 feet or even bigger in size; its structural properties similar to those of a concrete slab.
“So it's super strong, really high load and the really great advantage is it uses smaller lumber sizes, so you're able to use smaller tree harvests. It’s a more sustainable way of doing things,” De Freitas said.
Not only does mass timber construction present a sturdy, much lighter alternative to concrete, it also remains resilient in the face of fires and earthquakes.
Much of it has to do with physics.
If you were to start a campfire using just big logs without any kindling, you’d be hard-pressed to get it going. The reason? You’d be missing a key ingredient: oxygen.
“That’s kind of how the difference is between heavy timber or mass timber construction versus light frame timber, like stud frames, like you’re used to seeing,” De Freitas said. “The reason that stud framing combusts so easily is because there's a ton of air. It's a little bit of wood and a lot of air, which you need for combustion.”
Mass timber construction, on the other hand, uses very large, dense sections. What happens in a fire is the flames char the outside layer, which insulates the rest of the member and actually protects it from collapse and burning.
Steel, on the flipside – though it doesn’t burn by itself – is “like the least fireproof construction you can have because when steel gets hot, it loses all of its strength,” De Freitas said. “So it melts and it collapses.” That’s why steel-focused buildings are coated with spray-applied fireproofing materials.
When it comes to dealing with seismic activity, mass timber construction has made significant strides, too. Cross-laminated timber allows structures to utilize a diaphragm design for floors and roofs – a horizontal system that transfers earthquake and wind forces to vertical building components, De Freitas explained.
Under current California building code, cross-laminated timber is not yet recognized as a vertical shear wall element, though proponents of the practice hope that state regulators soon will give the green light. In the meantime, architects are using lightweight wood-construction shear walls or – for larger buildings – steel braces to make mass timber buildings earthquake-resilient.
“As the code evolves, that will allow us to start using CLT shear walls, as well,” said De Freitas, referring to cross-laminated timber.
And improvements in glue technology should ensure cross-laminated timber sticks around.
Beams and columns built out of engineered pieces of wood that have been glued together and laminated in layers, a finished product known as glulam, have been around forever. “But the advancement of the glue for the CLT recently has gotten a lot better,” said Reggie Stump, a Public Works senior architect who is involved with one of the Public Works-designed projects where the use of mass timber is being explored.

Mass timber fuels accelerated schedule for golf clubhouse
The first Public Works-led project using mass timber construction in San Francisco is set to open by spring. Meanwhile, Public Works architects on two other projects are actively pushing for mass timber elements.
Built from the ground up, the new Golden Gate Park Golf Course Clubhouse replaces a previous clubhouse that was badly damaged in a fire in 2018 and later had to be demolished. The new 1,560-square-foot facility, part of the beloved public nine-hole course, includes a restaurant, a bar, a large patio and a pro shop.

The new Golden Gate Park Golf Course Clubhouse is set to open by spring.
It’s poised to be the first public mass timber building Public Works has constructed in the City, said De Freitas, the project architect. Public Works handled design, engineering and construction management on behalf of Rec and Park.
“One of the drivers of why we're using mass timber here was we wanted to do an accelerated construction schedule,” De Freitas said. “Doing a mass timber roof system enabled us to plan for a tighter construction schedule on the project.”
The roof beams and roof decking were erected in roughly three days, he added.

Crews work on the clubhouse’s glulam roof beams.
Mass timber construction is built for speed because the parts arrive in huge, prefabricated slabs that are then put in place by crane or forklift. “They’re screwed together like an Erector Set and everything fits nicely,” De Freitas said.
As opposed to a stick-framed building or a masonry-built structure where much of the work happens on-site, mass timber construction components are factory-fabricated, allowing for extreme precision and a brisk pace.
The new clubhouse is a hybrid mass timber building, combining steel columns with a cross-laminated timber roof, glulam roof beams and wood frame shear walls for the lateral system. It uses Douglas fir.
Speed wasn’t the only consideration for the Public Works team. They wanted the new building to fit in well with its wooded surroundings in the northwest sector of San Francisco’s largest park.

The clubhouse’s butterfly roof is a mass timber construction.
“We’re nestled in this forest ecosystem,” De Freitas said. “And so we wanted to have a structure that really spoke about the forest.”
It also embodies the ethos of West Coast modernism.
"It's like a way of doing timber architecture in a regional way, in a local way, in a way that's meaningful for here,” De Freitas said.

A wooden lab amid the trees
Fostering a connection with nature also motivated architects to explore mass timber construction for the Millbrae Campus Improvement Project, which includes a 60,000-square-foot water quality lab that Public Works is building for the San Francisco Public Utilities Commission. The SFPUC runs the gravity-fed Hetch Hetchy water system that stretches from Yosemite to San Francisco.
Situated on a 15-acre campus off El Camino Real in Millbrae on the Peninsula, the project is poised to break new ground.
.png)
A rendering shows the proposed improvements on the SFPUC’s Millbrae campus.
Using mass timber for a lab was for a long time challenging because labs have huge technical requirements, said Abdel Qader Tarabieh, the Public Works project architect for the lab.
“Now I think there is more adaptation of how mass timber could be used in a lab – mechanically, electrically, structurally,” he said.
The two-story project, which also includes offices, is still in the early design phases but a grid system the architects are introducing is adaptable to be built with steel or wood. Based on the campus feeling and design, using wood fits well with the environment and establishes a visual connection with the existing main headquarters, which is a glulam structure, Qader Tarabieh said.
.png)
A rendering shows the water quality lab (on the left) amid existing trees.
The plan is to use glulams and cross-laminated timber or hybrid mass timber. Glass elements would help show off the wood interior. A big grove of redwood trees grows outside the building.
“It's about referencing the nature of that forest that this building is embedding itself into, referencing those material connections and emotions,” said De Freitas, the project lead for the Millbrae campus.
The lab building is expected to be completed in 2028. The rest of the improvements on campus are slated to be done by 2030.

Poor soil calls for light timber
In the City’s Bayview neighborhood, Stump, the Public Works senior architect, is looking to help City partners understand the benefits of mass timber construction.
Stump and his team are working on the SFPUC Southeast Plant Operations, Engineering and Maintenance Buildings project, bringing much needed improvements to the largest wastewater plant in San Francisco. Public Works structural and electrical engineers, as well as landscape architects, also are involved.
The project, located at Jerrold Avenue and Phelps Street, consists of a new mechanical maintenance building and a new three-story mixed-use structure with trade shops on the ground floor, crew lockers and showers on the second floor and office space for engineers on the third floor. The mixed-use building also includes a large break room, a wellness room and conference rooms.

A rendering shows the Southeast Plant Operations, Engineering and Maintenance Buildings project in the Bayview.
Stump and his team are proposing to use glulam columns and beams, a steel brace frame and CLT floors and roofs for both buildings. The architects will also present SFPUC colleagues with a more traditional steel and concrete option.
In addition to helping the SFPUC and the City pursue their goals for more sustainable practices and facilities, a reason mass timber construction would make sense at the site has to do with the poor quality of the soil, Stump said.
Because the soil consists of fill, the buildings will need to have concrete piers driven into the earth to lend the structures stability. Since mass timber construction is significantly lighter than concrete, a wood build would mean fewer piers and potentially save on construction costs.
“We know that the soil is bad, we know that typically mass timber buildings are lighter,” said Stump, who manages the Public Works architects’ SFPUC studio. “And so we've kind of worked through that logic.”

A rendering shows a street-level view of the Southeast Plant Operations, Engineering and Maintenance Buildings project.
Additionally, from an aesthetic standpoint, Stump and his team want to offer a welcoming respite to workers who are used to going into sewer manholes and wastewater concrete buildings every day.
“More of a relaxation place and more of a calming place,” he said. Warm wood over cold concrete.
During the coming months, Stump will work with SFPUC officials to see what option they would like to pursue. Construction on the project is currently slated to start in October 2025 and wrap two years later.

Trending toward timber
As rules and regulations catch up to advances in science and technology, the potential for mass timber construction in buildings is growing.
Not only are more public and private entities becoming increasingly conscious of reducing their carbon footprint when considering new projects, but recent building code changes now allow for mass timber construction to be used in multi-floor projects and high-rises – another incremental step toward making the building technique more mainstream.
“So that shift is getting even more attention from all the people who work in the built environment,” said Qader Tarabieh, the Public Works architect working on the Millbrae project.
And while mass timber may never fully replace steel and concrete, the more it is used, the more comfortable people may be incorporating it into their projects.
With manifold benefits, from potentially regionalizing construction supply chains to helping battle climate change, the most obvious advantage of mass timber construction may have to do with its nature – and our own.
“How people react to buildings that are made out of wood, or where you see wood, it's kind of deeply embedded in human psychology,” De Freitas said. “We react very differently, we behave differently, we perceive a building that is built out of a natural material in a different way. So there's a lot of really positive benefits to that.”


Public Works road repair crews lay down fresh asphalt on 19th Avenue near Ortega Street in the Sunset.
On the Right Road to Smoother Streets
San Francisco’s strategic approach to maintaining roads has paid off: The City’s independently rated Pavement Condition Index (PCI) score increased to 75, a rating deemed “good” by the regional Metropolitan Transportation Commission. This rating puts San Francisco at the top among large Bay Area cities.
San Francisco’s score, which covered calendar year 2023, was one point higher than the year before. The score hovered in the mid-60s during the early 2000s. But the City’s strong commitment to invest in roadway maintenance over the last 15 years has resulted in a steady rise in the pavement condition score.
Public Works, which oversees San Francisco’s Street Resurfacing Program, follows industry best practices by preserving streets in good condition instead of letting them deteriorate. This approach is the most cost-effective. Extending the life of a block in San Francisco that is in good condition can cost as little as $50,000. By comparison, the price to completely reconstruct a block in very poor condition can be as much as $500,000 or more.
Crews work on roadway resurfacing.
Public Works uses in-house Bureau of Building and Street Repair crews and outside contractors to perform the paving work. Last year, we resurfaced 503 blocks, adding to the total of more than 8,000 blocks of the City’s nearly 13,000 that have been resurfaced in the last 15 years.
When selecting which blocks to repave, the Street Resurfacing Program team considers a number of factors: roadway condition, use – streets with public transit and bike lanes, for example, are prioritized – and whether the paving project can be combined with other infrastructure projects, such as sewer upgrades. Geographic equity also is considered to make sure the street improvements benefit all neighborhoods.
San Francisco’s higher PCI score in 2023 came despite a series of severe storms that battered the streets early in the year. Consider that Public Works street repair crews filled 12,358 potholes in 2023, a nearly 18% increase from the year prior.
Over the past 15 years, Public Works’ employees and contractor crews resurfaced more than 8,000 blocks in San Francisco, including this one on Taylor Street in Nob Hill.
Even with the spike in numbers, Public Works crews responded to 91% of the 311 service requests for pothole repairs within 72 hours, besting the 90% service-level target. We also run a proactive pothole-repair operation that targets residential streets in neighborhoods throughout the City. The presence of potholes is one consideration in determining the PCI score.
San Francisco streets serve as core infrastructure, connecting communities, supporting commerce and expanding access. The improved PCI score underscores Public Works’ commitment to keep the roads well maintained for residents, visitors and businesses.
San Francisco’s PCI score, which is tracked by the independent Metropolitan Transportation Commission, rates roads from 0 to 100, with 0 being the worst, rutted and crumbling, and 100 the best, just freshly paved. The average PCI score in the Bay Area is 67. San Jose’s latest reported score is 71 and Oakland’s is 57.
Here’s the complete list of the City 503 blocks that got fresh paving last year.
The assessment was based on visual surveys performed by specially trained and certified staff. Each segment is evaluated based on ride quality, cracking and signs that the roadway may be breaking up in places.
The PCI rating represents a cumulative snapshot of all the streets that fall under the City’s maintenance responsibility. Looked at individually, the Metropolitan Transportation Commission evaluation found that two-thirds of San Francisco’s blocks are considered to be in “good” or "excellent” shape.


This multi-generational trio of volunteers didn’t toss litter along the Ocean Beach promenade, but they stepped up to pick it up, embodying community pride.
Volunteers Show Up Strong to #LoveOurCity
More than 125 community volunteers helped us kick off the 2024 season of Love Our City: Neighborhood Beautification Day events this month, planting trees, mulching and weeding medians, removing graffiti and tending to rain gardens in the Richmond District.
Organized by Public Works, the team of neighborhood stewards rotates through a different supervisorial district every month, January through November. Last year, Neighborhood Beautification Day events drew 940 participants who collectively contributed 3,290 hours of volunteer time.
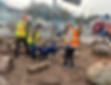

Neighborhood Beautification Day volunteers spruced up the outdoor gardens at Argonne Elementary School (left), while others wiped out graffiti across the Outer Richmond (right).
The year’s first event, held on Jan. 27, got underway with a rally at Argonne Elementary School in the heart of the Richmond. Volunteers were joined by Mayor London Breed and District 1 Supervisor Connie Chan who thanked the crowd for coming out. Then folks headed to their worksites.
Projects included planting trees along La Playa, sprucing up the Geary Boulevard median, picking up litter near the Great Highway, painting out graffiti along Balboa Street, mulching the sidewalk gardens near Argonne Elementary and more.
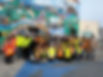
Mayor London Breed and Supervisor Connie Chan joined an energetic cadre of Public Works employees who came out on their day off to help beautify the Richmond District.
At each worksite, community volunteers – including many families – worked alongside Public Works landscapers, arborists and street cleaners. Taking care of San Francisco takes all of us working together to make the most meaningful difference.
We always welcome new volunteers and are thankful for those who keep coming back. To learn more about Love Our City: Neighborhood Beautification Day, including the 2024 calendar of events and how to get involved, visit sfpublicworks.org/volunteer.
Next month, on Feb. 10, we’ll be in Noe Valley and other District 8 neighborhoods. We hope to see you there!


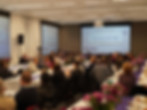
Public Works Director Carla Short kicks off this year’s Partnering Awards ceremony.
Sixth Annual
Collaborative
Partnering Awards
This month, Public Works hosted the 6th annual Collaborative Partnering Awards ceremony, which recognized nine City and County of San Francisco building and infrastructure projects that demonstrate the principles and success of structured collaborative partnering.
The partnering process brings together owners, designers and construction teams throughout the life of a project to maximize timeliness, economic efficiency and quality. Projects were judged by a panel of five City and industry professionals.
Awards were given to projects affiliated with five City agencies: San Francisco Public Works, San Francisco International Airport, San Francisco Municipal Transportation Agency, San Francisco Public Utilities Commission and the Port of San Francisco. The projects included a variety of publicly funded improvements, among them a bus rapid transit corridor, a pump station upgrade, a shoreline resiliency initiative and a new community center.
The Public Works Bureau of Architecture, Bureau of Landscape Architecture and Bureau of Engineering were involved in two of the winning projects: the Southeast Community Center and the Van Ness Improvement Project.
The partnering recognition event took place on Jan. 12 at the City’s 49 South Van Ness Ave. office building.
A hearty cheers to the winners!

Members of the Van Ness Improvement project team won a Partnering Award for best infrastructure project valued at more than $20 million.

Members of the Southeast Community Center project team won a Partnering Award for best building project valued at more than $20 million.
INFRASTRUCTURE – CATEGORY 1 (UNDER $20 MILLION)
-
Heron’s Head Shoreline Resilience Project (The Port of San Francisco)
-
Storm Drain Pump Station 1C Project (SFO)
-
12 KV Cable Replacement & System Upgrade Project (SFO)
INFRASTRUCTURE – CATEGORY 2 (OVER $20 MILLION)
-
Van Ness Improvement Project (SFMTA)
BUILDINGS – CATEGORY 1 (UNDER $20 MILLION)
-
Mariposa Dry Weather Pump Station Improvements Project (SFPUC)
-
Muni Metro East Maintenance Facility Boiler and HVAC Rehabilitation Project (SFMTA)
-
Rental Car Quick Turn Around Building Fire Sprinkler Replacement Project (SFO)
BUILDINGS – CATEGORY 2 (OVER $20 MILLION)
-
Southeast Community Center at 1550 Evans Project (SFPUC)
BEST IN THE CLASS
-
Storm Drain Pump Station 1C Project (SFO)